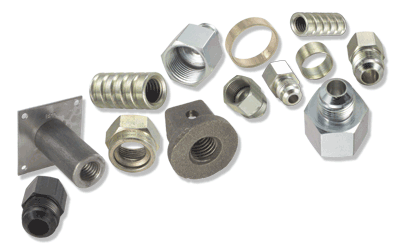
There are various methods for generating threads. The method selected for any one application is chosen based on constraints and available options; response time, cost, degree of precision, strength, and equipment availability, etc.
In general, certain thread-generating processes tend to fall along certain portions of the spectrum from custom to mass-produced tooling, there can be considerable overlap. For example, thread lapping following thread grinding would fall only on the extreme custom end of the spectrum, while thread rolling is a large and diverse area of practice with a wide range of application.
Threads of metal fasteners are usually created on a thread rolling machine. They may also be cut with a lathe. Rolled threads are stronger than cut threads, with increases of 10% to 20% in tensile strength and potentially more in fatigue and wear resistance.
Subtractive (Material Removal) Methods
Thread cutting
Thread cutting, as compared to thread forming and rolling, can be used when full thread depth is required, when the quantity is small, when the blank is not very accurate, when threading up to a shoulder is required, when threading a tapered thread, or when the material is brittle.
Thread tapping
Cutting with taps is a common method of threading. Unlike drill bits, taps do not automatically remove the chips they create. A tap cuts its threads in rotation creating long chips which can quickly jam the tap (an effect known as “crowding”), risking tool breakage.
For continuous tapping operations custom spiral point taps are used to break and eject the chips to prevent crowding.
Single-point threading
Single-point threading, more commonly referred simply as single-pointing, is an operation that uses a single-point tool to produce a thread form on or within a cylindrical or cone shaped item. The tool moves linearly while the precise rotation of the work-piece determines the leading edge of the thread. The process can be done to create external or internal threads (male or female). In external thread cutting, the piece can either be held in a chuck or mounted between two centers. With internal thread cutting, the piece is held in a chuck. The tool moves across the piece linearly, taking chips off the work-piece with each pass.
The coordination of various machine elements including lead screw, slide rest, and change gears were technological advances allowing the invention of the screw-cutting lathe, the origin of single-point threading as we know it today.
Horizontal and CNC lathes are the most commonly utilized equipment for single-point threading. CNC machines, process quickly and efficiently due the machine’s ability to constantly track the relationship of the tool position and spindle position. CNC software simplifies equipment set-up via pre-programmed subroutines that eliminate manual programming of a set-up cycle. Parameters are entered (e.g., thread size, tool offset, length of thread) via computer keypad operation or directly from the programmer’s pc, the machine does the rest.
All threading could feasibly be done using a single-point tool, but because of the high speed and low unit cost of other methods (i.e., tapping, die threading, thread rolling and forming), single-point threading is usually used when other factors of the manufacturing process favor it (i.e., low quantity demand, unique thread requirements, torque and/or horsepower preclude tapping, physical size, etc).
Thread milling
Threads may be milled with a rotating milling bit following a programmed helical tool path. Thread Milling is suitable for mass-production work, as such it is not common in job-shop work. With the widespread dissemination of affordable, fast, precise CNC machines, it has become much more common, internal and external threads are often milled on work that would have formerly been cut with taps, die heads, or single-pointing. Advantages of thread milling are faster cycle times, less tool breakage, and a left- or right-hand thread flexibility with the same tool. For large, awkward work-pieces, it is easier to let the work-piece sit stationary while all machining operations are performed with rotating tools.
There are various types of thread milling, including several variants of form-milling and combination of drilling and threading with a single tool.
Form-milling uses single- or multiple-form tools. One example of form-milling, the single-form tool is tilted to the helix angle of the thread and then fed radially into the blank. The blank is slowly rotated as the tool is precisely moved along the axis of the blank, cutting the thread. Achievable in one pass if the tool is fed to full thread depth, or in successive passes with lesser material removal. This process is typically used on larger threads. It is commonly used to cut large-lead or multiple-lead threads. A similar example using a multiple-form tool produces the complete thread in one revolution around the blank. The tool must be longer than the required thread length. Using a multiple-form tool is faster than using a single-form tool but it is limited in helix angle.
Yet another version of form-milling involves holding the tool’s axis orthogonally (no canting to the thread’s helix) and feeding the tool in a path generating the thread. The part is usually a stationary work piece, such as a boss on a valve body (external thread) or a hole in a plate or block (internal thread). This type of thread milling uses essentially the same concept as contouring with an end-mill, but the tool and path are arranged specifically to define the “contour” of a thread. The tool geometry reflects the thread pitch but not its lead. Tapered threads can be cut with either a tapered multiple-form tool that completes the thread in one revolution or with a straight or tapered single piece tool.
Tooling used for thread milling can be solid or indexable. For internal threads, solid tools are generally limited to holes larger than 0.24 in (6mm), indexable internal thread cutting tools are limited to holes larger than 0.47 in (12mm). The advantage; as the insert wears out it is easily and more cost effectively replaced. The disadvantage; cycle time is generally longer than solid tools. Solid multiple-form thread cutting tools look similar to taps, but they differ in the cutting edge does not have a back-taper and no lead-in chamfer. This lack of a lead-in chamfer allows the possibility of threads to be formed within one pitch length of the bottom of a blind hole.
Core-tapping
Core-tapping is the process of core drilling/threading internal threads using a special application cutting tool on a CNC mill or similar drive mechanism. The cutting tool tip is shaped like a drill, while the shank is thread shaped like a tap. The process advantage eliminates a tool change.. The disadvantage is the process is typically limited to hole depth no greater than three times the diameter of the tool.
Thread Whirling
Thread Whirling is a form of the Thread Milling process with the exception that cutting bits are mounted on the inside of a Cutting Ring or Tool Holder rather than the outside of a milling tool. Thread whirling offers several advantages over single point threading:
- Deep Threads – as with Bone Screws, usually have a deep thread formation similar to Acme forms and other increased pitch threads.
- Long Length to Diameter Threads – when used on a Swiss Type machine the whirling spindle works close to the guide bushing for increased support and rigidity on long length to diameter threads. The process is usually performed in a single pass from stock diameter which maintains constant material support.
- Faster Setup – by eliminating the need to match rough and finish insert forms, the whirling process reduces setup and fine adjustment time.
- Increased Productivity – cycle time reduction and increased run time results in greater productivity. Thread Whirling is usually performed in a single pass from stock diameter, eliminating multiple passes required for single point threading.
Deformative (Material Displacement) Methods
Thread forming and thread rolling
These are processes for forming threads, with the former referring to creating internal threads and the latter external threads. In both processes threads are formed into a blank by pressing a shaped tool, commonly called a €œthread rolling die€ against the blank, in a process similar to knurling. These processes are typically used for large production runs or specific applications when thread strength must meet a minimum yield. Forming and rolling produce no swarf (chips, shavings, etc), less material is required since the blank size starts smaller than a blank required for cutting threads. A rolled thread can often be recognized due the thread having a larger diameter than the blank from which it was produced; necks and undercuts can be cut or rolled onto blanks with threads that are not rolled.
Materials are limited to ductile materials because the threads are cold formed. The process improves the thread’s; yield strength, surface finish, hardness, and wear resistance. Materials with good deformation characteristics are necessary for rolling and likewise, exclude brittle materials.
There are four primary types of thread rolling, aptly named for the configuration of the process dies: flat dies, two-die cylindrical, three-die cylindrical, and planetary dies. The flat die system uses two dies, the bottom one is held stationary, while the second one slides. The blank is placed on one end of the stationary die, the moving die slides over the blank causing the blank to roll between the two dies forming the threads. Before the moving die reaches the end of its stroke, the blank rolls off the stationary die in a finished form. The two-die cylindrical process is used to produce threads up to 6 in (150 mm) in diameter and 20 in (510 mm) in length. There are two types of three-die processes; the first has the three dies move radially out from the center to let the blank enter the dies and then closes and rotates to roll the threads. This type of process is commonly employed on turret lathes and screw machines. The second type takes the form of a self-opening die head. This type is more common than the former, but is limited by not being able form the last 1.5 to 2 threads against shoulders. Planetary dies are used to mass-produce threads up to 1 in (25 mm) in diameter.
Unlike thread-cutting operations that use fluted taps, thread forming taps do not make chips. Instead, they displace or move material to form the shape of the thread. The taps have a polygonal cross section with forming wedges that mirror the thread profile. Their lead taper produces the thread profile, gradually flowing material from the thread crests, along the thread flanks and into the minor diameter area. Because the material is compressed and its grain is redirected, rather than cut or interrupted, strength at the thread flanks and root is increased.
Tapping via cold forming is appropriate for materials with tensile strength less than 1,200 N/mm2 and fracture strain of 5 percent. As a rule of thumb, if a continuous chip is created when drilling, the material is likely a good candidate for cold forming threads. However, suitable materials react to cold forming in different ways. The very reason thread forming taps have specific combinations of geometry and coatings to thread standard steels; soft steels; hardened steels; stainless steels; cast aluminum; wrought aluminum alloys and non-ferrous metals; and materials with limited ductility. Coatings include titanium nitride, titanium carbonitride and diamond-like amorphous carbon. Anti-friction coatings may also be used for materials such as wrought aluminum to prevent material from adhering to the tap.
Given the high amount of friction generated during the forming process, lubricants or emulsion coolants are recommended. Minimum quantity lubrication can also be used for certain applications. Some tool versions have through-tool coolant delivery to assist in threading blind holes. Others exit the tool coolant into longitudinal grooves to boost tapping speed and thread quality.
Threading Capabilities
Threads commonly produced by Hastings Machine Company include, but are not limited to: Unified National Coarse (UNC), Unified National Fine (UNF), National Pipe Thread (NPT), Coil, Metric, Tapered, Transitional (i.e. #8 to #10), Euro, ACME, 8 Round (API), etc.
Material capabilities run the gamut of: Cold Drawn Carbon Steel, Alloy, Stainless, Duplex, Aluminum, Brass, Cast Ductile Iron, and select Polymers.
Our threading capabilities include:
- Multi-Station Turntable Units
- Vertical and horizontal operations
- 1/4″ thru 2″ diameter capability
- Tapping and drilling heads
- Vertical drilling screw tapping heads
- Automatic handling
- Dedicated Vertical Tapping
- 1/4″ thru 2 3/8″ diameter capability
- 12″ stroke capabilities
- Multi-Spindle Vertical Drilling
- 1/4″ thru 2″ diameter capability
- Automatic Nut Tapping
- 1/2″ thru 1 3/8″ diameter capability
- Surface Grinding
- Fixed and multi-axis capabilities
- Automatic handling
- Band Sawing
- Machine Lathe
- Single spindle, horizontal support